Digitale Industrie 4.0 und das Industrial Internet of Things (IIoT) sind mehr als nur kryptische Begriffe. Sie betreffen uns alle – Unternehmen, Verbraucher und die Art und Weise, wie wir kommunizieren und produzieren. Bereits heute erleben wir tektonische Verschiebungen, die die Art und Weise, wie Dinge hergestellt werden, grundlegend verändern. Künstliche Intelligenz, Robotisierung, E-Commerce, virtuelle Realität, 3D-Druck, Biotechnologie und Cybersicherheit – all dies ist Teil der Digitalisierung in der Fertigung.
Wie Fortune Business Insights berichtet, wurde die Größe des globalen Marktes für digitale Transformation im Jahr 2023 auf 2,27 Billionen US-Dollar geschätzt. Der Markt wird von 2,71 Billionen US-Dollar im Jahr 2024 auf 12,35 Billionen US-Dollar im Jahr 2032 wachsen. Dies bedeutet eine jährliche Wachstumsrate von 20,9 Prozent über den Prognosezeitraum. Diese beeindruckenden Zahlen verdeutlichen die immense Bedeutung und das Potenzial der digitalen Transformation in der heutigen Wirtschaft.
In unserem Blogartikel “KI im Geschäftsleben: Eine neue Welle der Digitalisierung” berichten wir über die wachsende Bedeutung von KI in verschiedenen Branchen. In diesem Artikel wollen wir tiefer in das Thema KI in der Fertigungsindustrie eintauchen und einen Blick in die Vergangenheit werfen, um den Trend der heutigen Technologie besser zu verstehen.
Wir beginnen mit einer kurzen Einführung in die industrielle Revolution, um zu zeigen, wie jede Phase die Produktionsbranche transformiert hat.
Wir werden den aktuellen Stand der Industrie 4.0 beleuchten und erläutern die Rolle von IT- und Cloud-Lösungen in der modernen Produktion. Zudem betrachten wir die Bedeutung der Softwareentwicklung in diesem Kontext.
Die Entwicklung der Industrie: Von 1.0 bis 4.0
Angetrieben durch die Einführung neuer Technologien, repräsentiert Industrie 4.0 eine neue Ära vernetzter, robotergestützter und intelligenter Unternehmen. In dieser Phase der digitalen Revolution verschwimmen die Grenzen zwischen der physischen und der digitalen Welt. Dies führt zu einer neuen Art von vernetzten 4.0-Betrieben, in denen Menschen, Maschinen und Produkte in Echtzeit miteinander kommunizieren und interagieren.
Der Begriff “Industrie 4.0” wurde erstmals 2011 auf dem World Industry Forum in Hannover vorgestellt. Das Projekt “Industrie 4.0” oder “Industrie der Zukunft” steht für eine revolutionäre Denkweise in Bezug auf Produktionsmethoden. Die “4” symbolisiert die vierte industrielle Revolution.
Nun werfen wir einen Blick auf die Entwicklung der Industrie von den Anfängen bis zur heutigen Industrie 4.0.
Die Entwicklung der Industrie: Von 1.0 bis 4.0
Erste industrielle Revolution: Die Dampfmaschine
Die erste industrielle Revolution war von mechanischen Innovationen geprägt, insbesondere durch die Weiterentwicklung der Dampfmaschine durch James Watt im Jahr 1769. Diese Erfindung ermöglichte den Übergang von handwerklichen Manufakturen zur industriellen Massenproduktion.
Es dauerte einige Jahrzehnte, bis die Dampfmaschine sich weit verbreitete. Schließlich wurde sie jedoch unverzichtbar. Eisenbahnen und Dampfschiffe, die massenhaft produzierte Waren und Menschen transportierten, symbolisierten den Triumph dieser ersten industriellen Revolution.
Zweite industrielle Revolution: Die Elektrizität
Die zweite industrielle Revolution wurde durch die Einführung der Elektrizität angetrieben. Auch hier dauerte es eine Weile, bis das revolutionäre Potenzial dieser Technologie vollständig erkannt wurde. Zu Beginn des 20. Jahrhunderts begannen die Menschen allgemein, die Vorteile der Telegrafie zu erkennen. Sie sahen auch den Nutzen elektrischer Maschinen gegenüber Dampfmaschinen und der elektrischen Beleuchtung im Vergleich zu Petroleum oder Gas.
In den Fabriken markierte die Einführung des Fließbandes bei Henry Ford den Beginn einer neuen Ära. Die “mechanical assembly line” steigerte die Produktivität der Automobilherstellung enorm und machte individuelle Mobilität für breite Bevölkerungsschichten erschwinglich. Der Verbrennungsmotor trieb diese Neuerfindung, das Automobil, an. Zahlreiche Personen, die zuvor manuelle Arbeiten verrichteten, fanden neue Berufe als Elektriker. Andere begannen, am Fließband zu arbeiten.
Dritte industrielle Revolution: Der Mikroprozessor
Die dritte industrielle Revolution war digital. In den 1970er Jahren übernahmen Computer Aufgaben, die Menschen zuvor erledigten. Sie begannen, in vielen Bereichen menschliche Arbeitskräfte zu ersetzen. Der entscheidende technologische Durchbruch dieser Ära war die Entwicklung von Mikroprozessoren, die aus raumfüllenden Rechenmaschinen tragbare Geräte machten. Diese Technologie wurde schnell zur Universaltechnologie unserer Zeit – vom Personal Computer bis zur speicherbaren Steuerung, vom World Wide Web bis zur elektrischen Zahnbürste. Die pandemiebedingten Unterbrechungen der Chip-Lieferketten aus Asien offenbarten eine starke Abhängigkeit. Sie zeigten eindrucksvoll, wie sehr die Weltwirtschaft auf diese Technologie angewiesen ist.
Industrie 4.0: Die umfassende Digitalisierung
Industrie 4.0 steht für die umfassende Digitalisierung der industriellen Produktion. Diese Phase knüpft an die Errungenschaften der dritten industriellen Revolution an. Ihr Ziel ist es, die digitale Transformation in der Industrie umfassend umzusetzen.
Im Gegensatz zu früheren Revolutionen fehlte Industrie 4.0 ein einzelner, alles verändernder technischer Durchbruch. Es handelt sich eher um eine notwendige und längst überfällige Weiterentwicklung. Ihr Ziel ist es, die industrielle Produktion durch digitale Technologien effizienter und vernetzter zu gestalten. Es ist ein Schritt, der die bestehende Technologie weiterentwickelt und optimiert, um den Anforderungen der modernen Welt gerecht zu werden.
Was ist die Digitalisierung der Fertigung?
Die Digitalisierung in der Fertigung bezeichnet den Übergang zu einer vollautomatisierten, digital gesteuerten Fertigung, die in Echtzeit von intelligenten Systemen überwacht und mit ihrer Umgebung interagiert.
Dieser Wandel hin zur digitalen Fertigung erfordert die Schaffung einer mehrstufigen, integrierten IT-Infrastruktur. Diese Infrastruktur erleichtert die Transformation zahlreicher horizontaler und vertikaler Geschäftsprozesse, optimiert den Betrieb und verändert die traditionellen Modelle und Formen der Interaktion zwischen den Teilnehmern der Wertschöpfungsketten.
Im Kern der digitalen Transformation von Industrieunternehmen steht die Automatisierung von Prozessen und die Übertragung von Informationen in eine digitale Umgebung. Diese digitale Umgebung ermöglicht eine schnellere und einfachere Analyse von Daten, was wiederum präzisere und fundiertere Entscheidungen ermöglicht.
Vorteile der Digitalisierung für Industrieunternehmen
Die Einführung der Digitalisierung bringt für Fertigungsunternehmen eine Vielzahl von Vorteilen mit sich. Einige der wichtigsten Vorteile sind:
Steigerung der Effizienz
Durch die Digitalisierung können Produktions- und Technologieprozesse effizienter gestaltet und gleichzeitig die Kosten gesenkt werden. Ein kontinuierlicher Verbesserungsprozess ist ein wesentlicher Bestandteil der Digitalisierung. Technologien ermöglichen es Unternehmen, Ausfallzeiten von Produktionsanlagen zu minimieren, Wartungskosten zu senken, die Produktivität zu steigern, Produktionszykluszeiten zu verkürzen und Lagerkosten zu reduzieren.
Erhöhte Produktionsflexibilität
Zukunftsorientierte Unternehmen zeichnen sich durch ihre Flexibilität aus. Die Digitalisierung ermöglicht eine schnelle Anpassung an äußere Veränderungen. Sie erlaubt dynamische Änderungen im Produktionsprozess. Diese Flexibilität bietet Unternehmen einen Wettbewerbsvorteil, verbessert die Dienstleistungsqualität und steigert die Kundenzufriedenheit.
Reduzierung des Einflusses des Faktors Mensch
Durch die weitgehende Automatisierung und Robotisierung aller Prozesse verringert die Digitalisierung die Abhängigkeit von menschlicher Arbeitskraft. Dies führt zu geringeren Arbeitszeitverlusten, weniger Ausschuss, schnellerer Informationsübertragung und -verarbeitung, schnelleren Entscheidungsprozessen und einer höheren Produktqualität.
Erhöhte Sicherheit
Die Digitalisierung in der Fertigung erhöht die Sicherheit in Produktionsstätten erheblich. Dank der kontinuierlichen Überwachung wird die Anzahl der Unfälle deutlich reduziert. Zudem erhöht sich das Schutzniveau der Mitarbeiter. Verletzungen werden verringert und schädliche Produktionsfaktoren minimiert.
In unserem Artikel “Die transformative Rolle der KI in Unternehmen” haben wir bereits die Vorteile des Einsatzes von Künstlicher Intelligenz (KI) am Beispiel der Lebensmittelbranche der Firma Kellogg’s erläutert. Hierbei wurde deutlich, wie KI zur Effizienzsteigerung und Optimierung von Produktionsprozessen beitragen kann.
Insgesamt bietet die Digitalisierung Industrieunternehmen eine Vielzahl von Vorteilen, die zu einer effizienteren, flexibleren und sichereren Produktion führen.
Kernelemente von Digitale Industrie
Industrie 4.0 basiert auf einer Vielzahl von technologischen Innovationen, die zusammen eine umfassende digitale Transformation der industriellen Produktion ermöglichen. Zu den zentralen Elementen gehören:
Schlüsseltechnologien in der Industrie 4.0
- Internet der Dinge (IoT):
Vernetzung von Maschinen, Geräten und Sensoren, die miteinander kommunizieren und Daten austauschen. - Künstliche Intelligenz (KI), maschinelles Lernen und Robotik:
Automatisierung und Optimierung von Produktionsprozessen durch intelligente Systeme, die aus Daten lernen und sich anpassen können. Beispiele hierfür sind Prognosen, Defekterkennung und Materialklassifizierung.
Durch maschinelles Lernen und fortgeschrittene Algorithmen können KI-Systeme Produktionsprozesse kontinuierlich analysieren und optimieren. Sie identifizieren Muster in Produktionsdaten. So können sie etwa die Produktionsgeschwindigkeit für maximalen Durchsatz anpassen oder den Energieverbrauch durch Modifikation der Arbeitsschritte optimieren. - Cloud Computing:
Bereitstellung von Rechenleistung und Speicherressourcen über das Internet, um flexible und skalierbare IT-Infrastrukturen zu schaffen. Beispiele hierfür sind die verteilte Speicherung der Daten und die hohe Verfügbarkeit der Daten. Cloud Computing eröffnet Industrie 4.0 neue Möglichkeiten für flexibles Arbeiten und dezentrale Arbeitsstrukturen. Durch die Vernetzung von Systemen und die Nutzung von Cloud-Computing können Mitarbeiter an verschiedenen Standorten zusammenarbeiten und auf relevante Daten zugreifen. Dies ermöglicht eine erhöhte Flexibilität bei Arbeitszeit und -ort und fördert die Vereinbarkeit von Beruf und Privatleben. - Big Data:
Analyse großer Datenmengen, um Muster zu erkennen, Prognosen zu erstellen und fundierte Entscheidungen zu treffen. - Additive Fertigung:
Herstellung von dreidimensionalen Objekten durch schichtweises Auftragen von Material, auch bekannt als 3D-Druck. - Cybersicherheit:
Schutz von IT-Systemen und industriellen Netzwerken vor Cyberangriffen und Datenverlust. Beispiele hierfür sind die Erstellung von Konnektivität weltweit über Fabriken mit geschützter Verbindung. - Integrationssysteme:
Verknüpfung verschiedener IT-Systeme und Prozesse zu einer nahtlosen, integrierten Produktionsumgebung. - Modellierung:
Erstellung digitaler Zwillinge und Simulationen, um Produktionsprozesse zu planen, zu überwachen und zu optimieren. - Erweiterte Realität (AR):
Nutzung von Technologien, die digitale Informationen in die physische Welt einblenden, um Arbeitsprozesse zu unterstützen und die Effizienz zu steigern.
Diese Kernelemente sind die Bausteine von Industrie 4.0 und ermöglichen es Unternehmen, ihre Produktionsprozesse zu digitalisieren, zu vernetzen und zu optimieren.
Herausforderungen der Digitalisierung in der Fertigung
Die Digitalisierung in der Fertigung macht die Produktion flexibler, anpassungsfähiger und wettbewerbsfähiger. Unternehmen können genau feststellen, was der Markt zu einem bestimmten Zeitpunkt braucht. Sie passen ihre Produktion entsprechend an.
Die digitale Transformation soll verschiedene Probleme adressieren, wie:
- Geringe Produktivität:
Durch Automatisierung und Optimierung der Prozesse wird die Effizienz gesteigert. - Irrationale Ressourcennutzung:
Digitale Systeme helfen, Ressourcen effizienter zu nutzen und Verschwendung zu minimieren. - Hohe Produktionskosten:
Durch die Reduzierung von Ausfallzeiten und Wartungskosten können die Gesamtkosten gesenkt werden. - Geringe Effizienz der Produktionsanlagen:
Echtzeitüberwachung und prädiktive Wartung verbessern die Leistung und Lebensdauer der Anlagen.
Die Digitalisierung in der Fertigung verbessert die Marktposition eines Unternehmens. Sie ermöglicht eine schnellere Markteinführung und steigert die Produktqualität. Maßgeschneiderte Produkte können mit derselben Effizienz wie in der Massenproduktion hergestellt werden, was die Kundenzufriedenheit erhöht.
Digitale Systeme integrieren alle internen und externen Prozesse eines Produktionsunternehmens in einem einzigen virtuellen Raum. Dies ermöglicht eine umgehende Informationsbeschaffung und die Echtzeitüberwachung der Arbeit, wodurch die Verwaltung effizienter, einfacher und transparenter wird.
Komplexitäten des KI-Einsatzes in der Produktionsbranche
Künstliche Intelligenz bietet viele Vorteile. Doch bei der Digitalisierung in der Fertigung stehen wir vor Herausforderungen. Diese müssen wir bewältigen:
- Datenqualität und -verfügbarkeit:
Hochwertige Daten sind entscheidend für die Leistungsfähigkeit von KI-Systemen. Unvollständige oder fehlerhafte Daten können die Ergebnisse verfälschen. - Integration in bestehende Systeme:
Die Einbindung von KI in bestehende Produktionssysteme kann komplex und kostspielig sein. - Datensicherheit:
Es ist essenziell, sensible Daten vor Cyberangriffen zu schützen. Dies gilt besonders, wenn Produktionsprozesse digitalisiert und vernetzt sind. - Fachkräftemangel:
Es besteht ein hoher Bedarf an qualifizierten Fachkräften, die in der Lage sind, KI-Systeme zu entwickeln, zu implementieren und zu warten. - Regulatorische Anforderungen:
Die Einhaltung gesetzlicher Vorschriften und Standards kann eine Herausforderung darstellen, insbesondere in stark regulierten Branchen.
Unsere Lösungen
Innovaforge bietet umfassende Lösungen, um die Herausforderungen der Digitalisierung und des KI-Einsatzes in der Produktionsbranche zu meistern. Wir unterstützen Sie bei der Implementierung und Optimierung digitaler Systeme, die Ihre Produktionsprozesse effizienter, flexibler und sicherer machen. Mit unseren maßgeschneiderten Lösungen helfen wir Ihnen, die Vorteile der Digitalisierung voll auszuschöpfen und Ihre Marktposition zu stärken.
Wir helfen auch bei der Cloud-Migration von Berichtssystemen, die zur Steuerung von Produktionslinien in Industrie 4.0 genutzt werden. Dank unserer Expertise integrieren wir Ihre Systeme nahtlos in die Cloud. Dies ermöglicht eine verbesserte Skalierbarkeit, Verfügbarkeit und Datensicherheit.
Eine detaillierte Fallstudie zu unserer Arbeit finden Sie unter folgendem Link: Carl Zeiss Fallstudie.
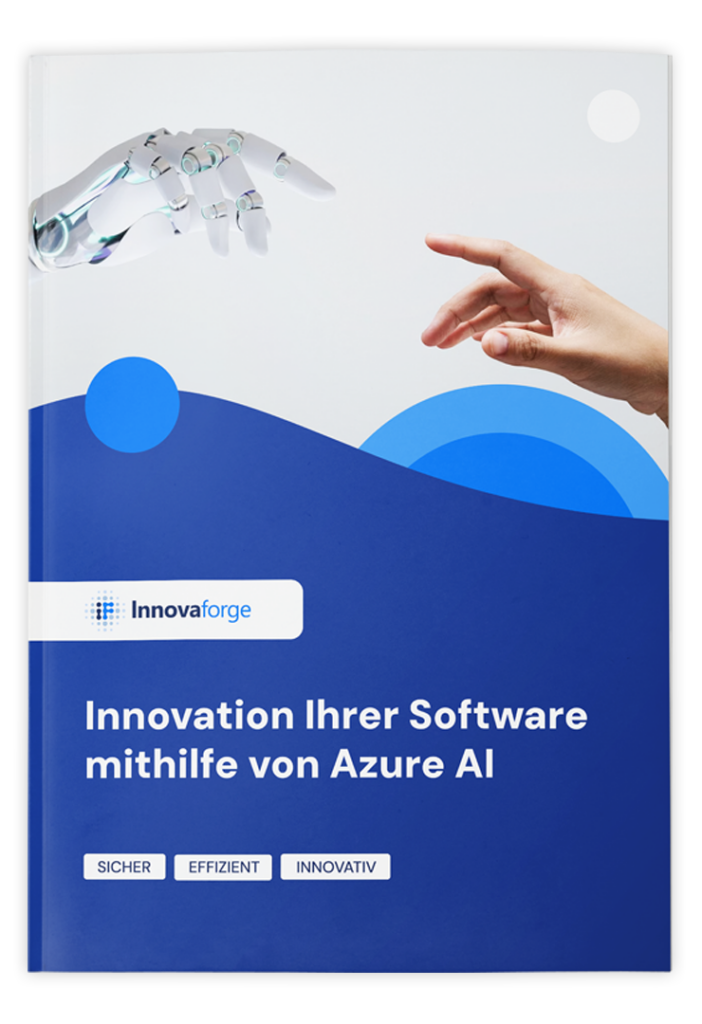
Für noch mehr Informationen zum Thema KI-Einsatz in Unternehmen bieten wir ein kostenloses Whitepaper zum Download an. Dieses Whitepaper enthält wertvolle Einblicke und praxisnahe Tipps, wie Sie KI erfolgreich in Ihre Produktionsprozesse integrieren können.
Besuchen Sie auch unsere LinkedIn-Seite, um aktuelle Informationen und Neuigkeiten zu erhalten. Hier teilen wir regelmäßig Beiträge und Artikel rund um die Themen Digitalisierung und Künstliche Intelligenz in der Industrie.
Zögern Sie nicht, einen Termin mit uns zu vereinbaren. Unsere Experten stehen Ihnen zur Verfügung, um Ihre spezifischen Anforderungen zu besprechen und maßgeschneiderte Lösungen für Ihr Unternehmen zu entwickeln.